The **Essential Guide to Plastic Mold Making**
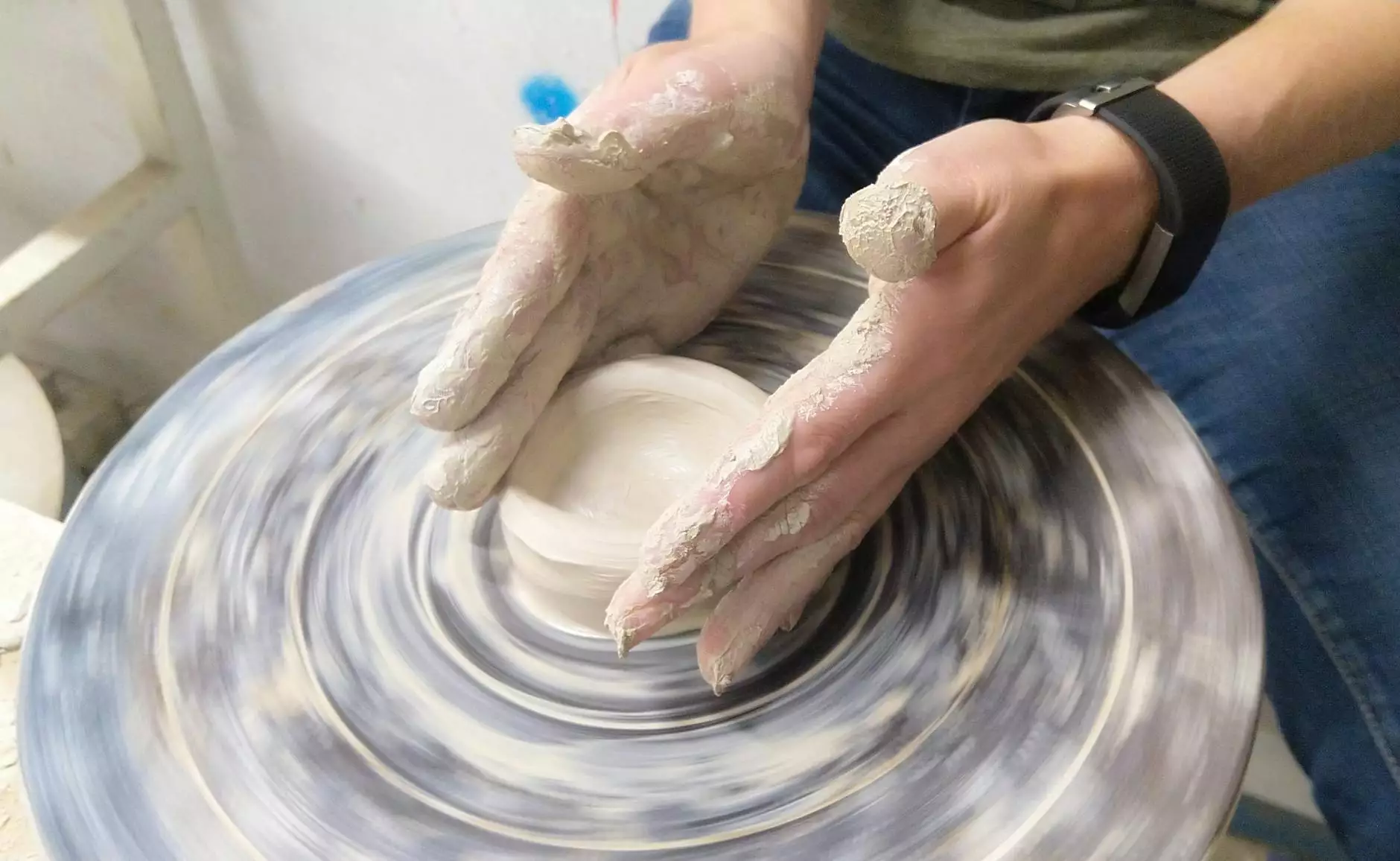
The world of manufacturing is vast and varied, but one area that stands out in its importance and complexity is plastic mold making. This technical process is the backbone of many industries, producing everything from small consumer goods to essential automotive components. In this extensive guide, we’ll explore the ins and outs of plastic mold makers, with special emphasis on their significance, advantages, and applications in the modern industrial landscape.
What is a Plastic Mold Maker?
A plastic mold maker is a specialized manufacturer that designs, builds, and maintains molds used in injection molding processes. The mold is a hollow metal block that is shaped in such a way that it defines the final shape of the product. Once the mold is created, raw plastic material is injected into the mold under high pressure, allowing it to fill the space and take on the desired form once cooled.
Key Responsibilities of a Plastic Mold Maker
- Designing Molds: Collaborating with engineering teams to design molds that meet precise specifications.
- Building Molds: Utilizing CNC machinery, manual tools, and other equipment to construct molds.
- Testing and Prototyping: Performing rigorous testing to ensure the molds produce quality parts without defects.
- Maintenance: Regularly servicing molds to prevent wear and tear and extending their lifespan.
The Importance of Choosing the Right Plastic Injection Mould Manufacturer
Choosing the right plastic injection mould manufacturer is critical for businesses aiming to maintain a competitive edge in their respective markets. Here's why:
1. Quality Assurance
Quality molds lead to quality products. A reputable plastic mold maker adheres to stringent quality standards, ensuring that every item produced is consistent and reliable.
2. Cost Efficiency
Investing in high-quality molds may seem expensive upfront, but they can significantly reduce production costs in the long run. Well-made molds enhance the efficiency of the manufacturing process and minimize defects, which can otherwise lead to costly reworks.
3. Technical Expertise
Experienced mold makers possess in-depth knowledge of materials and processes, enabling them to provide valuable insights and recommendations tailored to your unique needs.
Understanding the Process of Plastic Mold Making
Step 1: Design and Prototyping
The process begins with designing the mold. This phase involves:
- 3D Modeling: Using CAD software to create a 3D model of the component to be produced.
- Simulation: Running simulations to predict how the plastic will flow and fill the mold.
Step 2: Mold Fabrication
Once the design is approved, mold fabrication can commence. This includes:
- Machining: Cutting, milling, and shaping the components of the mold from high-quality steel or aluminum.
- Assembly: Assembling the machined parts into a complete mold unit.
Step 3: Testing and Adjustments
The assembled mold is then tested by producing sample parts. This step involves:
- Trial Runs: Conducting injection trials to evaluate the mold's performance.
- Adjustments: Making any necessary adjustments to achieve the desired quality and dimensional accuracy.
Step 4: Production
Upon successful testing, the mold is ready for mass production. Key factors during production include:
- Monitoring: Careful monitoring of the injection process to ensure quality and consistency.
- Maintenance: Regular maintenance checks to prevent any operational issues.
Advantages of Working with an Expert Plastic Mold Maker
Engaging with experienced plastic mold makers provides businesses with several advantages:
1. Custom Solutions
Custom molds are tailored to specific applications, providing a perfect fit for your products. Experienced mold makers can create bespoke solutions that meet unique project requirements.
2. Speedy Turnaround
Established manufacturers have refined their processes to offer quicker lead times without sacrificing quality. This efficiency enables faster time-to-market for your products.
3. Advanced Technologies
Utilizing state-of-the-art technology and innovative techniques, professional mold makers remain at the forefront of the industry, employing methods like:
- 3D Printing: Rapid prototyping to expedite the design process.
- High-Speed Machining: Enhancing production efficiency and mold precision.
Applications of Plastic Molds in Various Industries
Plastic molds find applications across a multitude of industries, showcasing their versatility:
1. Automotive Industry
Molds are used to create essential components such as dashboard panels, bumpers, and interior fixtures, ensuring durability and aesthetic appeal.
2. Consumer Products
Many everyday items, from plastic bottles to food containers, rely on molds for mass production. The ability to produce high volumes at low costs makes it ideal for the consumer goods sector.
3. Medical Devices
Precision and safety are paramount in the medical field. Plastic molds producing components for medical devices undergo rigorous quality assurance to comply with health regulations.
4. Electronics
Plastic housings and components for electronic devices, such as smartphones and tablets, are produced using advanced molding techniques, ensuring functionality and aesthetic design.
Challenges in Plastic Mold Making
While the benefits of working with a plastic mold maker are immense, there are challenges inherent in the process:
1. Cost of Materials
The cost of high-quality raw materials for mold making can fluctuate, impacting budgets. It's crucial to find a manufacturer that balances quality with cost-effectiveness.
2. Technical Complexity
The complexity of mold design requires sophisticated engineering skills and knowledge. Picking a skilled mold maker is essential to navigate these complexities.
3. Market Competition
The demand for plastic manufacturing is high, meaning businesses often face intense competition. Continuous innovation and quality improvement are necessary to stay ahead.
Choosing the Right Partner: What to Look for in a Plastic Mold Maker
When selecting a plastic mold maker, keep the following factors in mind:
- Experience: Look for manufacturers with a solid track record and experience in your specific industry.
- Portfolio: Evaluate their previous work to ensure their style and quality align with your expectations.
- Certification: Ensure they comply with relevant industry certifications that guarantee quality and safety.
- Customer Service: Choose a company that prioritizes communication and customer support throughout the production process.
Conclusion
In conclusion, the role of a plastic mold maker cannot be overstated. Their expertise and craftsmanship are essential to producing high-quality plastic components that drive modern industries. By understanding the intricacies of plastic mold making and the advantages of partnering with a reputable plastic injection mould manufacturer, businesses can ensure they are well-equipped to meet the demands of their markets.
For businesses looking to embark on their journey of plastic manufacturing, understanding these elements is crucial. Make informed decisions, utilize expert knowledge, and embrace the innovations in the field to secure a successful venture. Selecting a reliable partner, especially in the domain of plastic mold makers, can set the foundation for lasting success and growth in your operations.