Lifting Equipment LOLER Cardiff: Ensuring Safety in Your Operations
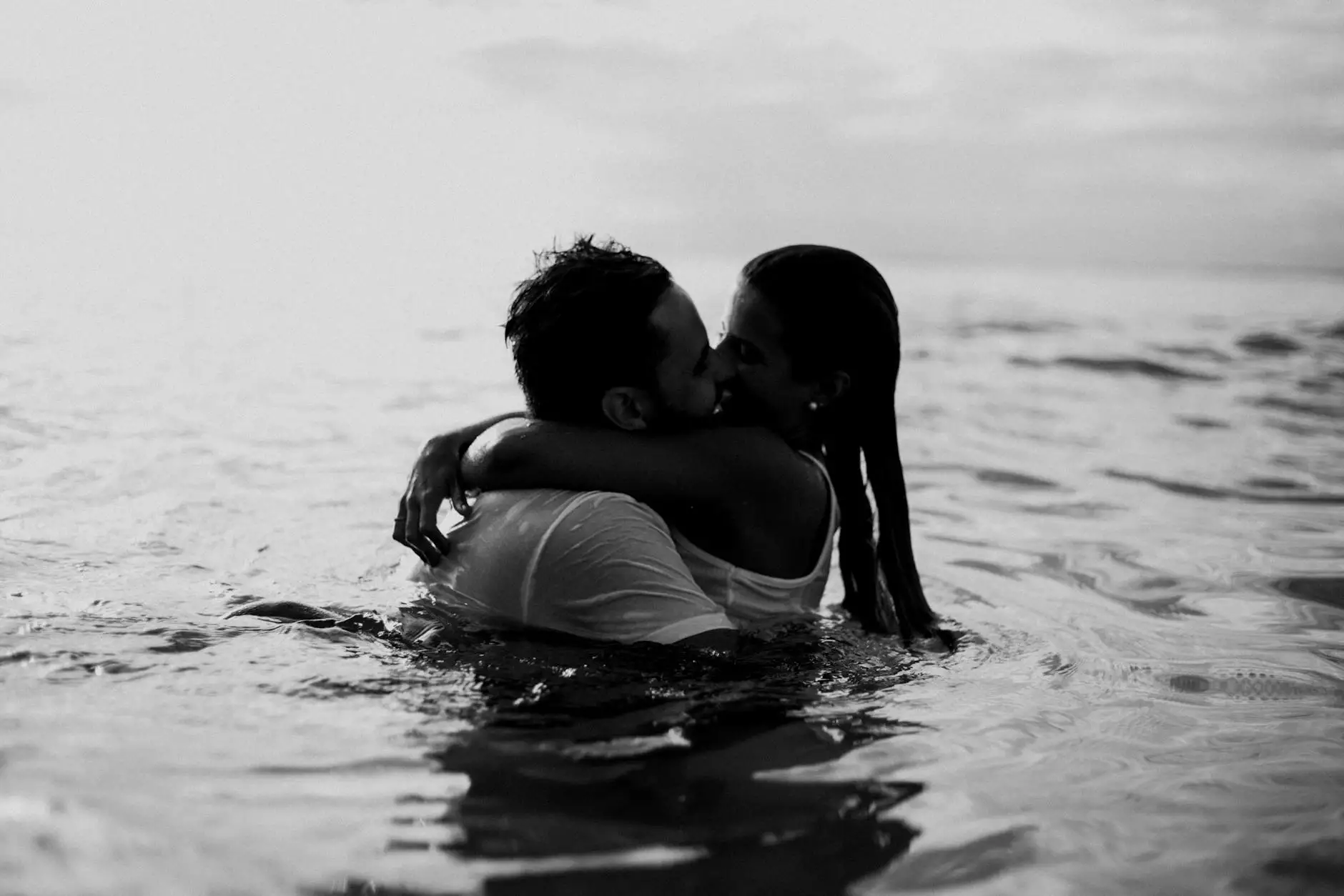
The effective utilization of lifting equipment is crucial for numerous industries, from construction to manufacturing. In Cardiff, understanding the LOLER (Lifting Operations and Lifting Equipment Regulations) standards is essential for any business that engages with lifting machinery. This article provides comprehensive insights into the importance of lifting equipment, how LOLER regulations enforce safety, and how Safe Plant UK can support your business's compliance needs.
Understanding Lifting Equipment and Its Importance
Lifting equipment comprises a wide range of machines and devices designed to lift, lower, or move loads. This equipment includes but is not limited to:
- Cranes
- Forklifts
- Hoists
- Elevators
- Slings
Every business that utilizes lifting equipment must prioritize safety and compliance with regulations. In Cardiff, a city bustling with industrial activity, the proper management of lifting operations is not just a legal obligation; it is a core component of operational excellence.
What is LOLER and Why is It Crucial?
The LOLER regulations were established to ensure that lifting operations are carried out safely and efficiently. The key objectives of LOLER include:
- Ensuring that lifting equipment is suitable for the intended use
- Maintaining the safety of lifting operations
- Reducing the risk of accidents and injuries
- Establishing regular inspections and maintenance of lifting equipment
In Cardiff, compliance with LOLER standards is critical for avoiding hefty penalties and enhancing safety across workplaces. Businesses must ensure that their lifting equipment meets both operational and regulatory requirements to protect their workforce and assets.
Lifting Equipment Inspections: What You Need to Know
Regular inspections of lifting equipment are a fundamental aspect of LOLER compliance. These inspections help to identify any potential hazards and ensure that all equipment is safe for use. Safe Plant UK provides expert inspection services in Cardiff, assisting businesses in meeting their LOLER obligations effectively. Here’s what you need to know about the inspection process:
Frequency of Inspections
LOLER dictates that lifting equipment must be thoroughly examined:
- At least once every 12 months for lifting equipment
- For lifting accessories, the examination must occur at least every 6 months
- Whenever the equipment is modified or if an incident occurs
Regular inspections are vital not only for legal compliance but also for maintaining operational efficiency and worker safety.
The Inspection Process
The inspection process typically includes the following steps:
- Visual Inspection: A thorough visual check for signs of wear, damage, or corrosion.
- Functional Testing: Checking that all mechanisms work correctly and safely.
- Documentation Review: Ensuring all previous inspection records are up-to-date and accessible.
- Compliance Assessment: Verifying that the equipment meets all appropriate safety standards.
By partnering with Safe Plant UK, you can ensure that your lifting equipment inspections are conducted by certified professionals, minimizing the risk of non-compliance.
How Safe Plant UK Can Help Your Business
Safe Plant UK specializes in providing comprehensive support for all things related to lifting equipment and LOLER compliance in Cardiff. Here’s how we can assist your business:
Expert Consultation
Our seasoned professionals offer expert consultation to help businesses understand their obligations under LOLER. We assess your current lifting operations and provide tailored recommendations to enhance safety and compliance.
Training Services
Your employees are your most valuable asset. We provide LOLER training sessions designed to educate workers about safe lifting practices, equipment handling, and regulatory compliance. Investing in training is essential for fostering a culture of safety within your organization.
Equipment Supply and Maintenance
Safe Plant UK not only offers inspection services but also supplies a range of lifting equipment that meets LOLER standards. Furthermore, we provide ongoing maintenance services to ensure that your equipment remains in optimal condition.
The Impact of Non-Compliance
Failure to comply with LOLER regulations can lead to severe consequences, including:
- Legal Penalties: Businesses can face substantial fines and legal action.
- Increased Risk of Accidents: Non-compliance often leads to unsafe working conditions, risking employee safety.
- Reputation Damage: Non-compliance can harm your business reputation, leading to lost clients and opportunities.
Given these risks, prioritizing lifting equipment safety and compliance is not just a best practice; it is an essential business strategy.
Conclusion
In summary, the safe operation of lifting equipment under the LOLER regulations in Cardiff is crucial for protecting your workforce and assets. By engaging with professionals like Safe Plant UK, businesses can ensure that they are compliant with all relevant safety standards while also improving operational efficiency.
Investing in proper lifting equipment management, inspections, and training not only fulfills legal obligations but also fosters a culture of safety and accountability within your organization. Don't risk the safety of your employees or the integrity of your operations; partner with Safe Plant UK to ensure your lifting operations are both safe and compliant with LOLER standards.
Contact us today to learn more about how we can assist with your lifting equipment compliance needs in Cardiff.
lifting equipment loler cardiff